Maped : retour d’expérience avec Autodesk Simulation Moldflow
Depuis 2002, MAPED fait appel à Simulation Moldflow pour concevoir ses outillages et a ainsi développé un moule pour produire des bannettes courrier en PET bouteille recyclé. Ce produit a reçu en Allemagne le prix European Office Product Awards (EOPA) du meilleur produit écologique de l’année.
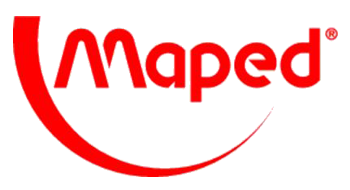
L’entreprise Maped (Haute-Savoie) est parmi les leaders mondiaux des accessoires scolaires (compas, gommes, taille-crayons, ciseaux, instruments d’écriture, traçage) et de bureau (agrafeuses, perforateurs, articles de rangement…) . Créée en 1947, Maped fabriquait à l’origine des compas en laiton et des petits mécanismes pour appareils photos. « Nous étions des mono-spécialistes du compas jusqu’en 1985 où l’actuel président Jacques Lacroix a pris la main et décidé d’élargir le rayon d’action de la société ». Celle-ci passera d’un chiffre d’affaires de 15 millions de francs en 1985 à 160 millions d’euros consolidé groupe aujourd’hui. En 1993, Maped tout en continuant de maîtriser totalement la chaine de conception, a installé une usine en Chine afin d’accroitre sa compétitivité sur différents produits « Cette délocalisation en Asie a permis de créer de nouveaux emplois, au sein même du service R&D France. En 1999, il y avait 8 personnes en R & D, aujourd’hui, nous sommes 25 ! ».
A Pringy, Maped s’appuie sur des équipes dédiées, c'est-à-dire qu’en Open Space, l’entreprise dispose de la totalité de la chaîne de développement Produit avec notamment deux designers intégrés, une équipe de développement packaging et une unité prototype intégrée avec des imprimantes 3D, des fraiseuses… » Parfois, un acheteur de la grande distribution vient nous voir le lundi et en fin de semaine, désire recevoir une réponse à son appel d’offres avec à minima un design propre, quelquefois des prototypes physiques. Si l’on veut tenir les délais, il nous faut impérativement garder ce service en interne pour disposer d’un packaging imprimé avec un traceur, une découpe de carton et un produit prototypé ou imprimé 3D et peint».
Autodesk Simulation Moldflow pour concevoir les outillages du premier coup
L’entreprise dispose de plusieurs sites de production en Allemagne, Chine, Argentine, Mexique avec environ 120 machines d’injection pour 2 000 tonnes de plastique transformées. « Cela peut paraître peu important pour les gros transformateurs, mais lorsque vous avez des taille-crayons de 2 gr, cela représente 100 millions de taille-crayons. Sur le marché de l’écriture, nous employons des moules 24/32 empreintes avec des temps de cycle de 15 à 20 secondes. Les matières sont de type ABS, polypropylène, polycarbonates, polyamides et les matériaux recyclés ».
Le Service R & D de Maped s’est équipé d’Autodesk Simulation Moldflow en 2002. « Là encore, nous n’avions pas le choix ! Les grands groupes de distribution qui représentent jusqu’à 20% de notre chiffre d’affaires viennent nous consulter en Octobre-Novembre pour une livraison de produits en Mai et il y 6 semaines de livraison en bateau. Face à ces délais, nous ne pouvons pas nous permettre de faire de multiples itérations avec nos outillages. C’est tout l’intérêt de la simulation ! Chez Autodesk Simulation Moldflow, il y a un vrai savoir-faire, des modules extrêmement intéressants, des packages très attractifs. C’est un outil universel par rapport à certains de ses concurrents, enfin, il y a un atout très apprécié : le langage d’utilisation en français ».
En 2002, Maped fait ses premiers pas avec une licence Simulation Moldflow avec 3 utilisateurs. Aujourd’hui, huit utilisateurs disposent d’une licence Autodesk Moldflow Insight (AMI), d’une licence Autodesk Moldflow Adviser (AMA), de 3 licences d’exploitation graphique Moldflow Synergy et d’une station dédiée au calcul en réseau. L’intégrateur Aplicit a conseillé Maped pour le choix de ce solveur uniquement dédié à Insight, ce qui permet d’augmenter la productivité puisque tout le monde peut lancer des calculs et disposer assez rapidement des résultats. « Nous proposons la meilleure solution matériel adaptée aux besoins en calcul du client tout en respectant ses critères économiques » souligne Cédric Ségard, Ingénieur d’Application Simulation chez Aplicit Lyon. « En règle générale, il est rare de voir autant d’utilisateurs sur un même site. Chez Maped, la simulation, c’est vraiment un travail quotidien »
Mettre le logiciel à la portée de tous les utilisateurs
Au début la R & D s’appuyait sur quelques experts en simulation. Mais aujourd’hui, grâce aux dernières solutions proposées par Autodesk Simulation Moldflow, beaucoup d’utilisateurs l’utilisent directement sur leur poste. « Nous avons estimé qu’il existait plusieurs niveaux d’un logiciel de simulation et nous avons essayé de mettre le logiciel à la portée de tous les utilisateurs. Nous avons une vraie gestion intuitive et conviviale du logiciel, que ce soit adviser (AMA) ou Insight (AMI). Nous avons 5 à 6 personnes qui ont moins de 25 ans et il faut qu’ils s’attribuent très vite les outils grâce à une prise en mains rapide. Pour les débutants, l’objectif est d’éviter les grosses bêtises au point d’injection quand on commence les pièces en CAO » poursuit François Aznar. La pièce sort des mains des designers et du logiciel de design ; sur cette première CAO non dépouillée, le concepteur vérifie alors qu’il n’y a pas de pièges avec Adviser. « Nous avons mis au point des règles d’utilisation avec des « warnings » pour dire attention, vous avez 70 bars de pression, venez nous voir. Les utilisateurs plus expérimentés ou les référents experts qui maitrisent la simulation et l’injection dans l’atelier reprennent alors ces études sur Moldflow Insight ».
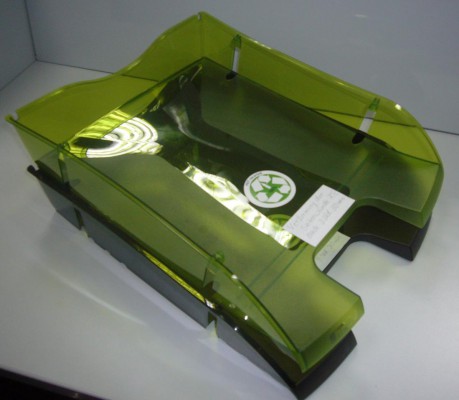
Cette méthodologie se conjugue avec la formation réalisée à la fois en interne et par des intervenants extérieurs. C’est l’intégrateur Aplicit à Lyon qui intervient alors en proposant des journées de rappel comme l’explique Cédric Ségard, ingénieur d’application simulation : « Pour les utilisateurs avancés, nous réalisons même des formations adaptées en fonction des demandes des concepteurs. L’objectif, c’est qu’ils obtiennent la meilleure utilisation du logiciel par rapport à leurs attentes ».
Un cas d’étude : la bannette de courrier en PET recyclée
En 2006, Maped reprend la société allemande Helit (usine à Berlin) qui fabrique des accessoires de bureau, des bannettes, des porte-documents avec 150 000 unités produites/an. L’objet de l’étude Moldflow est une bannette courrier incassable en polystyrène Crystal, d’une épaisseur assez fine et avec des chemins d’écoulement importants. « L’objectif était, sans en modifier les formes, de réaliser cette bannette courrier en PET 100% recyclé issu de la récupération des bouteilles d’eau à un prix intéressant » souligne Jean Bardet, Expert plastique du Groupe Maped. « Moldflow nous a permis de dégrossir et d’aller assez loin dans la préconisation du design des outillages commandés ; nous avons pu corréler les résultats pour ce produit grand public qui est vendu 1,50 euros ».
La première approche a été de réaliser plusieurs pièces pour comprendre l’injection délicate de ce PET Bouteille plutôt prévu pour l’extrusion : par exemple, il faut maîtriser la dessiccation sinon la pièce peut casser ou des bouchons peuvent se former au niveau de la vis d’injection, maîtriser la température du moule pour éviter le blanchiment de la matière et les collages au niveau du moule, la température de la matière et le temps de séjour dans la vis qui doit rester assez court. Ensuite, la conception de l’outillage devait permettre d’injecter correctement la pièce avec des circuits de refroidissement optimisés, une maîtrise des canaux chauds.
En complément des essais, il s’est avéré nécessaire de réaliser une étude Moldflow. « La première approche a été au niveau de la matière avec un R-PET qui existe dans la base de données. Mais tous les essais avaient été effectués avec un matériau N 067 avec des résultats très proches et lors des premières simulations sur Moldflow, j’ai retrouvé des résultats plus fiables » poursuit Jean Bardet. « Au départ, nous avons corrélé les résultats existants avec la bannette polystyrène avec une pression de 440 bars, une force de fermeture de 400 tonnes sachant qu’aujourd’hui cette bannette est injectée sur une presse de 275 tonnes. On peut estimer que les résultats réels sont 30% au-dessous de la valeur exprimée dans Moldflow. Ensuite, nous avons voulu valider les autres paramètres comme le temps de refroidissement (6 secondes) avec un circuit de refroidissement que nous avons reproduit, un cycle total de 18 secondes et une déformée acceptable de +/- 1,3 mm puisque ces produits sont empilables ».
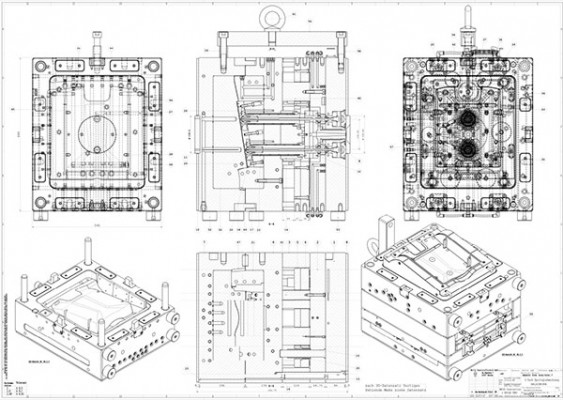
Simulation Moldflow : un formidable vecteur pour convaincre moulistes et injecteurs
Ce qui intéressait le service R & D, c’était surtout la pression d’injection maximale car Maped dispose d’un parc de presses de 275 à 380 tonnes. « Nous avons regardé des solutions avec 1 point d’injection et jusqu’à 4 points d’injection. Chez nous, lorsque l’on reste en dessous de 50 bars, il n’y a aucun souci. De 50 à 70 bars, on se pose des questions et l’on cherche à rééquilibrer les points d’injection. Au-dessus de 70 bars, les études précédentes ont montré qu’il y a un petit danger et l’on doit intervenir pour réduire cette pression. Enfin, au-delà de 100 bars, on ne lance pas l’outillage ».
Les résultats des simulations étaient les suivants : avec un point d’injection, la pression atteint 114 bars. Deux points d’injection donnent 71 bars et 4 points d’injection, 47 bars mais avec des problèmes comme les lignes de soudure et emprisonnements d’air. « J’ai proposé une très bonne solution en injection séquentielle avec 37 bars et une force de fermeture de 160 tonnes. Mais, en Allemagne, les experts injection qui produisent ces bannettes depuis plus de vingt ans n’ont pas voulu se lancer dans cette opération qui supposait des investissements importants ».
Le service R & D revient alors à la solution deux points d’injection en reprenant l’étude pour vérifier les températures : la température noyau varie de 44 à 68° avec des points très chauds peu acceptables dans les angles. « Nous avons rajouté un circuit de refroidissement sur les parois avec une eau à 15° qui nous a donné une température de noyau de 45° largement acceptable. Et un temps de cycle maîtrisé de 7 secondes au lieu de 6 auparavant. Nous avions cependant un souci avec une hausse de température au niveau des points d’injection et avons décidé de refroidir le moule au plus proche du problème. Enfin, nous avons vérifié la déformée qui restait dans le même écart acceptable ».
Maped lance alors l’outillage avec ses préconisations et travaille en collaboration avec le mouliste, l’entreprise allemande, les injecteurs, le fabricant de canaux chauds, pour définir le meilleur moule. « Le logiciel Autodesk Simulation Moldflow nous a permis de convaincre les divers intervenants, c’est très pédagogique » ajoute François Aznar. « Car il peut vous arriver de faire des préconisations qui ne rencontrent pas l’adhésion de tous » Il a fallu ensuite 4 mois pour réaliser le moule et le temps de cycle a été optimisé au bout de 4 mois. En 2011, l’entreprise allemande Helit a injecté 40 tonnes, en 2012, 100 tonnes et en 2013, 140 tonnes. Et cette corbeille à courrier Greenlogic a reçu le prix European Office Product Awards (EOPA) du meilleur produit écologique de l’année, pour l’injection de PET 100% recyclé issu de la récupération des bouteilles d’eau.
Interrogé sur le retour sur investissement du logiciel, François Aznar avoue qu’il est très difficile d’avancer des chiffres mais donne cependant une comparaison édifiante : « avant l’emploi de Moldflow, nous avions 3 à 4 modifications liés aux problématiques d’injection sur les moules. Aujourd’hui, lorsque nous en avons une ou deux, c’est le bout du monde. Et nous évitons aussi beaucoup d’erreurs et de pièges de conception »
En conclusion, François Aznar rappelle que la simulation est avant tout un outil d’interprétation : « Attention, ce n’est pas la vérité ! Nous insistons bien au niveau de nos collaborateurs. Certains viennent nous voir en disant, j’ai un retrait de 1,3 mm, peut-on le ramener à 1,1 mm ? Pour le faire, il faudrait maîtriser de façon absolue les outillages, la matière… Nous n’avons pas voulu nous lancer dans cette voie. Autodesk Simulation Moldflow est un formidable vecteur pour convaincre moulistes et injecteurs. A tel point que parfois, ce sont eux qui sont demandeurs ». Pour le futur, le service R & D de Maped s’intéresse aux solutions Autodesk sur le cloud. « Ce pourrait être une bonne solution pour nous, à la fois en gain de temps de calcul puisque les ressources sont quasi illimitées mais également au niveau des prestations. Par exemple, nous pourrions avoir accès à des logiciels pas ou peu utilisés. En disant cela, je pense à la mécanique des fluides pour étudier la circulation de l’eau dans une empreinte ».
Schneider Electric
Aplicit : des experts à la pointe de l’utilisation d’Autodesk Moldflow | Entretien avec Youssef Yousfi, Responsable Modélisation Simulation
Coffrage Equipage
Coffrage&quipage conçoit les éléments de coffrage sur Inventor et sous-traite ensuite la fabrication à des ateliers partenaires. Ils gèrent le suivi de la fabrication juqu'à la livraison afin d'apporter une solution « clé en main ».
Schneider Electric France
Virginie Renavant a 5 homologues sur les thermoplastiques et thermodurs. Elle est la seule de l’équipe à avoir une mission rhéologique et, à ce titre, est l’unique utilisatrice d’Autodesk Moldflow Insight et Synergy.
Chambre d’Agriculture de la Charente
Stéphane Bireau, conseiller Bâtiment durable certifié HQE a intégré de nouvelles technologies : Autodesk Advance Steel et le plugin TwinMotion en lien avec Autodesk Revit.
UIOSS de la Sarthe
L’UIOSS est en capacité de réaliser de la maintenance, de la rénovation et des travaux neufs. Pour mener à bien ces travaux, Frédéric Vallée a fait confiance à Autodesk Revit et au BIM.